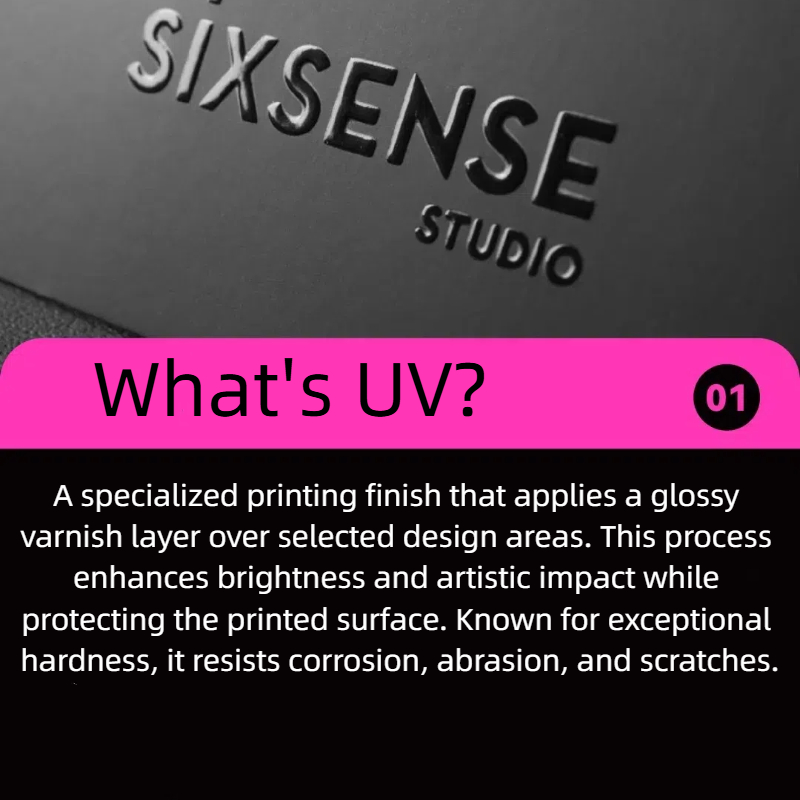
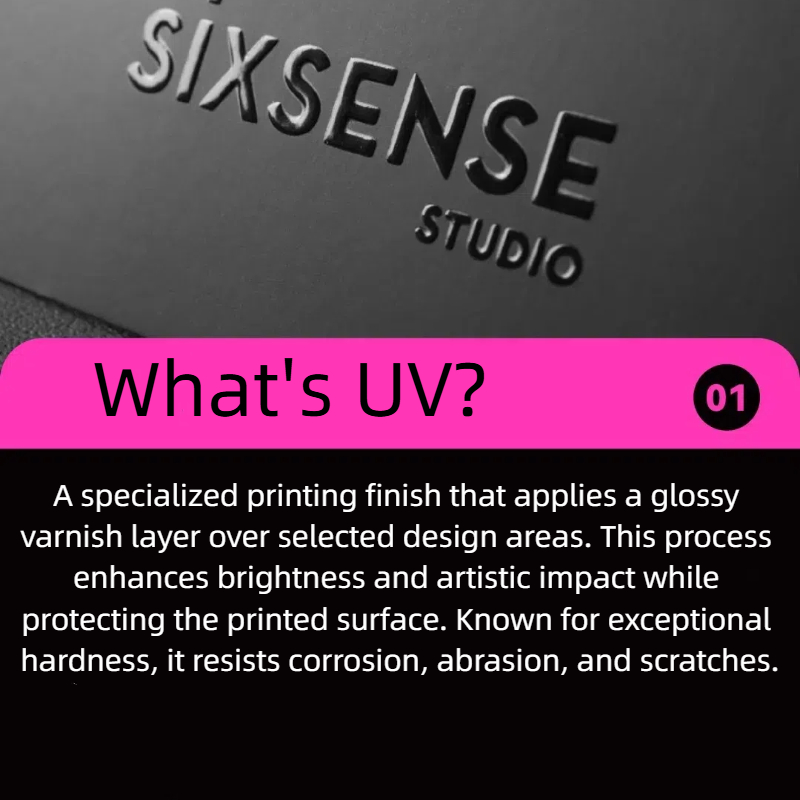
UV
A specialized printing finish that applies a glossy varnish layer over selected design areas. This process enhances brightness and artistic impact while protecting the printed surface. Known for exceptional hardness, it resists corrosion, abrasion, and scratches.
Special UV inks are applied via UV printing presses, enabling selective or full-surface coating. The ink is instantly cured by ultraviolet light, forming a raised, lustrous layer that adds pronounced dimensionality and contour definition to graphics.
UV printing is a digital or offset process that uses ultraviolet (UV) light to instantly cure specially formulated inks or coatings. Unlike traditional methods requiring drying time, UV curing creates durable, high-gloss finishes in seconds.
Key Technical Advantages
Feature | Benefit |
---|---|
Instant Curing | Prints are immediately ready for finishing/packaging → Reduces production time |
Versatile Substrates | Bonds to non-porous materials (plastic, metal, acrylic, foil) beyond paper/board |
Enhanced Durability | Resists scratches, chemicals, fading & moisture → Ideal for packaging exposed to logistics/storage |
Precision Effects | Enables spot gloss, textured effects (e.g., braille), and 3D-like raised printing |
Eco-Friendly | UV inks contain near-zero VOCs → Reduced environmental impact vs. solvent-based inks |
Process Workflow
Ink Application: UV-reactive inks deposited via print head/roller.
UV Exposure: Passed under high-intensity UV lamps.
Polymerization: Inks instantly harden via photochemical reaction.
Output: Fully cured, scratch-resistant print ready for use.
Industry Applications
Premium Packaging: Spot-gloss logos, scratch-resistant cosmetic boxes
Industrial Labels: Chemical/weather-resistant barcodes on drums
Signage & Displays: Glossy graphics on PVC/acrylic
Security Printing: Tamper-evident features on pharmaceutical packs
Tactile Effects: Braille on healthcare packaging
UV Printing vs. Conventional Printing
UV Printing | Traditional Printing |
---|---|
Instant curing | Hours/days for ink drying |
High adhesion to plastics/metals | Limited to porous materials |
Vibrant color saturation | Colors absorb into substrate |
Thicker ink layers for texture | Flat finish |
Higher upfront cost | Lower machine investment |
Technical Considerations
Energy Use: UV lamps consume significant power → LED-UV systems reduce energy by 70%
Material Compatibility: Test substrates for yellowing under UV exposure
Cost Factor: 20-30% higher ink cost offset by reduced waste/labor
Safety: Requires ozone ventilation and operator eye protection
Real-World Example:
Luxury perfume boxes use spot UV to make logos "pop" against matte laminates, while beverage labels leverage UV’s moisture resistance.
UV printing merges efficiency with premium aesthetics, making it indispensable for high-value packaging and functional print applications.