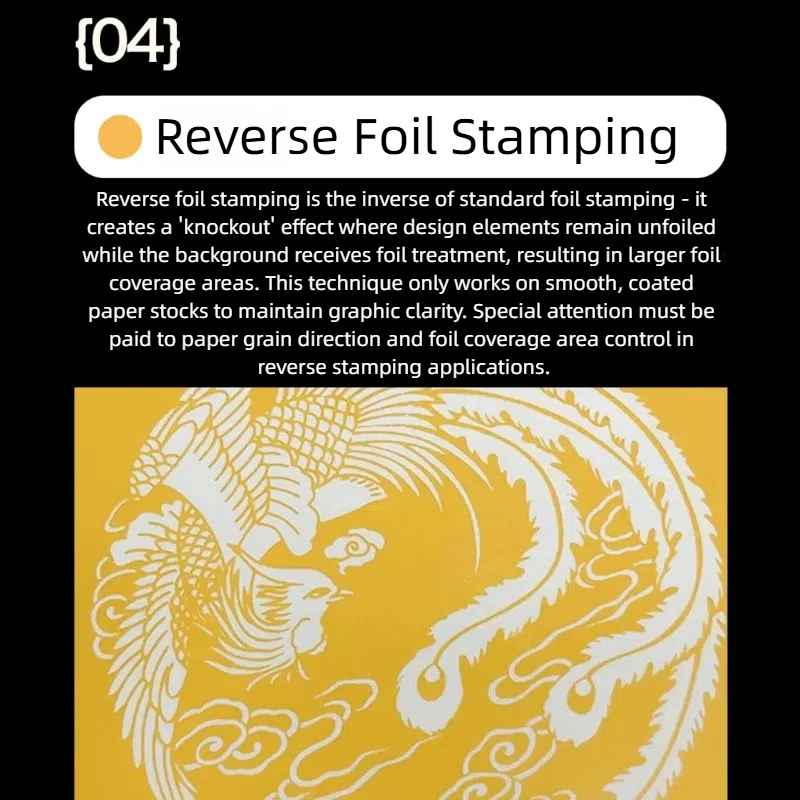
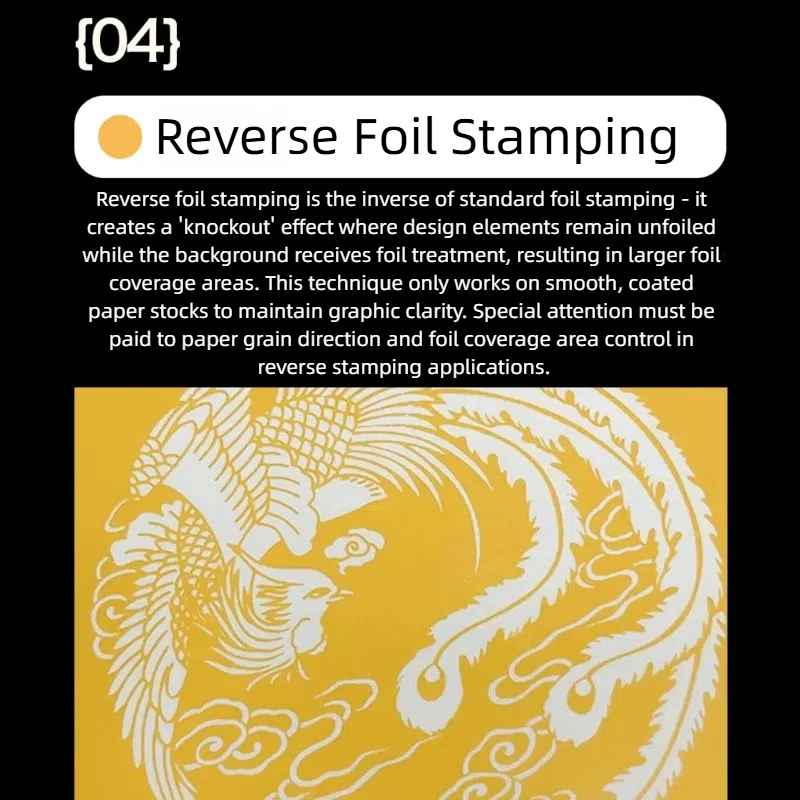
Reverse Foil Stamping
Reverse foil stamping is the inverse of standard foil stamping - it creates a 'knockout' effect where design elements remain unfoiled while the background receives foil treatment, resulting in larger foil coverage areas. This technique only works on smooth, coated paper stocks to maintain graphic clarity. Special attention must be paid to paper grain direction and foil coverage area control in reverse stamping applications.
Reverse foil stamping (also called negative foil stamping) is an advanced technique where foil is applied to the background of a design, leaving the main elements unfoiled (knocked out). This creates high-contrast metallic effects with sharp, clean edges.
Key Features
✔ High Visual Impact – Bold metallic backgrounds with uncoated negative space
✔ Design Flexibility – Works with intricate logos, typography, and patterns
✔ Anti-Counterfeiting – Difficult to replicate precisely due to registration demands
✔ Premium Perception – Used in luxury packaging for a sophisticated look
Common Applications
Luxury Branding
Champagne/wine labels (e.g., foil-background with matte-text logos)
High-end cosmetic packaging (e.g., black foil with negative-space brand names)
Security Features
Micro-text foil backgrounds on pharmaceutical boxes
Holographic reverse foil for authentication
Minimalist Designs
"Hidden" metallic effects (e.g., foil reveals light angles)
Contrast textures (matte unfoiled elements vs. glossy foil)
Sustainable Packaging
Partial foil coverage reduces material usage vs. full foil stamping
Process Workflow
Design Preparation
Artwork must have clear positive/negative separation
Foil area typically covers 60–90% of the design
Die Creation
Precision-etched brass dies (tolerances ≤0.05mm)
Silicone counterforce plates for even pressure
Stamping Execution
Temperature: 110–140°C (depends on substrate)
Pressure: 25–40 kg/cm²
Speed: Slower than flat foil for perfect registration
Substrate Compatibility
Best for smooth, coated stocks (e.g., art paper, laminated boards)
Avoid porous/uncoated materials (foil adhesion issues)
Technical Comparison: Reverse vs. Standard Foil
Factor | Reverse Foil Stamping | Standard Foil Stamping |
---|---|---|
Foil Coverage | Background only | Design elements only |
Registration | Critical (±0.1mm tolerance) | Less stringent (±0.3mm) |
Cost | 20–30% higher (precision dies) | Lower |
Effect | Negative-space metallic glow | Direct metallic elements |